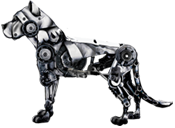
Disk Machining, Cleaning and Bedding-in New Brake Pads
Machine discs using the slowest feed rate with minimal depth to prevent grooving. For final clean-up use a solvent such as the spray-on ABS "brake cleaner". Do not use an oil based solvent.
Machining may leave a fine film of graphite on the surface that could affect breaking. Use the spray-on ABS "brake cleaner". Never use petrol for cleaning!
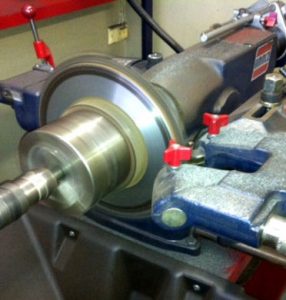
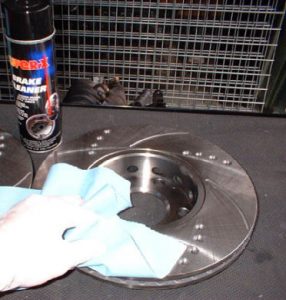
After fitting, once again wipe down the disc with a clean rag and the spray-on ABS Brake Cleaner.
Bedding-in is always advisable to condition material surfaces correctly. At 60 kph apply brakes using light to moderate pedal effort reducing to 10 kph. Do this at least 10 times.
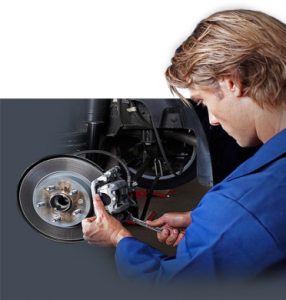
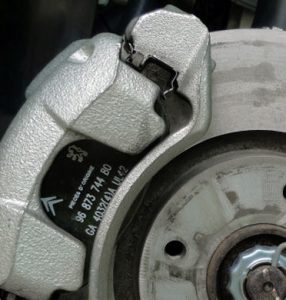
Brakes
On ABS brake systems, did you know that you should always clamp the brake hose and open the brake bleeder screw before you push back the caliper pistons when fitting new pads? If you don't, you will push all the OLD and CONTAMINATED brake fluid back up to the master cylinder and through the ABS valve system, where it could jam the valves at considerable cost to you and the customer. Using three of the ABS brake hose clamps will prevent this possibility.
Steering
Watch out for loose fan or pump belts, as this will cause slipping and reduces the power from the pump to the rack & pinion or box, thus giving you hard steering and a squealing noise on full lock. Fit a Magnefine filter for longer life and 99.99% cleaner oil. Partially worn suspension ball joints and tie-rod ends affect wheel alignment. For longer tyre life renew them with Nu-Tech.
Brake Fluid
Brake fluid is corrosive and poisonous. Keep it away from skin and eyes. Do not allow brake fluid to splash on painted surfaces.
Asbestos
Older brake friction materials, as well as dodgy Asian imports, contain asbestos - a known carcinogen. Brake assemblies can produce small airborne particles of asbestos during cleaning, which are easily inhaled. Breathing these particles may cause asbestosis, emphysema or lung cancer. The following safety rules should be observed at all times:
- Never use compressed air to blow brake assemblies clean. Use a contained vacuum cleaning system or flush with cleaner or water.
- When some exposure might be unavoidable, wear an approved filter mask.
Rotor Fitting Tips
- Compare the new rotors to the ones that have been removed to ensure they are correct. Some vehicles, such as Holden Commodores, have had running changes made to the brake system and may have different size rotors fitted.
- If the rotor is a removable hub type, clean the hub surface on to which the router will be mounted. The assembly surfaces must be free from rust, flat and free of burns. When tightening the hub bolts on this type rotor ensure that bolts are tightened to the manufacturer's recommended torque using the correct pattern. Over tightening of these bolts by using an impact gun will distort the new rotor, causing runout and in some cases the rotor will fracture.
- The face of the new rotor has protective coating applied. This must be removed by using an acetone or trichloroethylene based solvent. Using petrol or other type products will leave a residue of oil or wax affecting the braking performance.
- When re-fitting the new rotors, use a torque wrench to tension the wheel bearings to manufacturer's specifications. Torquing the wheel bearings correctly will prevent excessive disc rotor runout.
- Disc pads should only be replaced in axle repairs. A mixture of friction material can affect the braking performance.
- Inspect the front steering and suspension components for wear or damage. Problems in this area may cause vibrations or pulsations during braking, giving the impression the rotors have excessive runout or disc thickness variation.
- Ensure the master cylinder is operating correctly. If the master cylinder is holding pressure it will cause the rotors to overhead and distort.
- On ABS equipped vehicles, ensure the rotor supplied has the same number of teeth on the pole ring as the rotor you have removed. Fitting rotors with different numbers of teeth on the pole rings may cause increased stopping distances or a fault to be logged in the ABS system.
- If the new rotor has been supplied without the pole ring fitted, the old pole ring must be removed and re-fitted on the new rotor. Ensure the pole ring runout is within the manufacturer's specification after re-fitting the pole ring.
- When removing and re-fitting rotors on ABS equipped vehicles, take care to prevent the pole ring striking the tip of the wheel speed sensor. The wheel speed sensor may be damaged causing a fault to be logged in the ABS system.